. . . . . . . . . . . . . . . . . . . . . . . . . . . . . . . . . . . . . . . . . . . . . . . . . . . . . . . . . . . . . . . . . . . . . . . . . . . . . . .
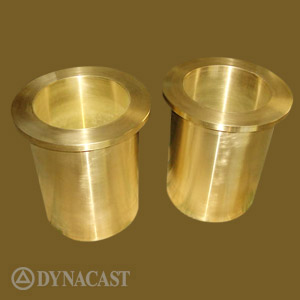
|
Material :
SAE 40; CDA 836
Minimum Hardness 60BHN @ 500kg Load
Size :
Available in Various Sizes |
|
|
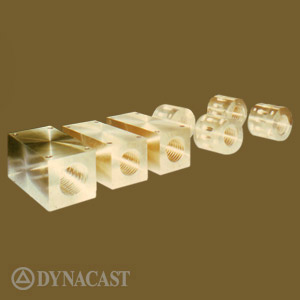
|
Material :
Manganese Bronze SAE 430-B; C863
Minimum Hardness 195BHN @ 3000kg Load
Size :
Available in Different Sizes |
|
|
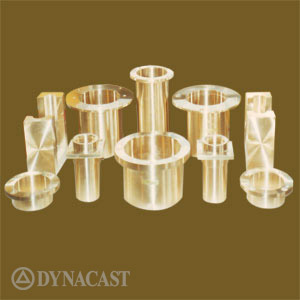
|
Material :
SAE 63/JIS BC2/BC3 (Material Match to Hardened Steel)
Size :
Available in Various Sizes |
|
|
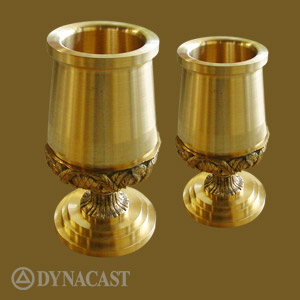 |
Material :
SAE 40, ASTM B505, CDA 836
Typical Uses:
SAE 40, Tiger Bronze are versatile, all-purpose bronze alloy that can be easily machined. It is preferred bronze alloy of choice as replacement due to its versatility, consistency and unmatched reliability. |
|
|
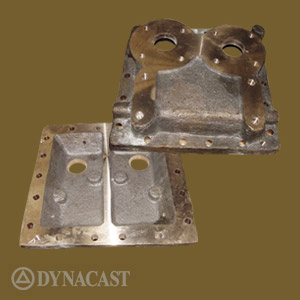 |
Material :
SAE 40, ASTM B505, CDA 836
Typical Uses:
SAE 40, Tiger Bronze are versatile, all-purpose bronze alloy that can be easily machined. It is preferred bronze alloy of choice as replacement due to its versatility, consistency and unmatched reliability. |
|
|
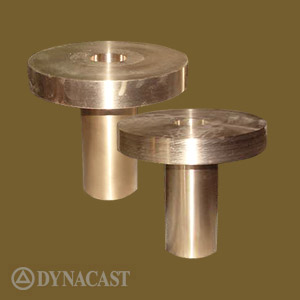 |
Material :
Hi-Grade Phosphor Bronze SAE 65 ASTM B505, CDA907
Typical Uses:
Phosphur Bronze combine good strength with high fatigue resistance without having to conpromise on its machinability, use under severe conditions, heavy-pressure bearings and bushing to use against hardened steel. |
|
|